

Our project team made several trips to their facility to see the dredges built, talked through challenges they have seen, the type of quality they expect, and more. The process was not new to our team, as we have completed MTR reports for numerous customers upon request.Īs the global leader in the design and build of dredges and dredge machinery, Ellicott worked closely with us throughout the project. These qualities are necessary for proper compliance, reporting, and application purposes. An MTR is a certified record of a material’s physical and chemical properties. The Material Test Report (MTR) was also crucial to the process for Ellicott because of the 316L stainless steel and the highly corrosive environment for the dredge’s end use. We could also use our seam welder, an automated welding process, to provide a consistent and clean look. Unlike other contractors, we had the in-house capabilities to roll and form the length and thickness of stainless steel needed for the barge. Due to the stainless-steel material, heavy welding was needed, which was no problem for our more than 60 certified welders with more than 200 welding certifications. WE DISCOVER:Įllicott was looking for a contractor to perform the weld standards at the highest quality.
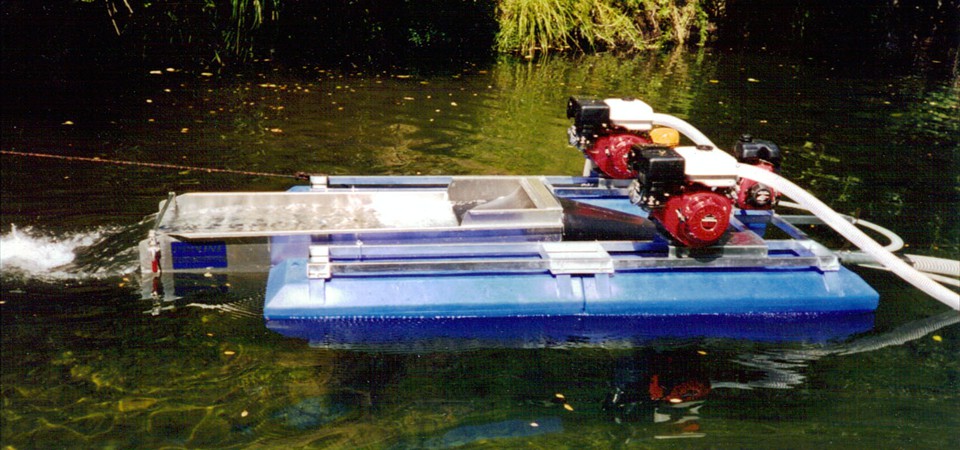
The dredge was to be fully welded, passivated, and watertight.

The project was a 90,000-pound, 18-foot-wide by 52-foot-long and 9-foot-tall 316L stainless steel dredge barge hull. Due to the material specifications, Ellicott didn’t want to make this type of dredge in-house, so they reached out to a qualified, experienced contractor. WE LISTEN:Ī new customer – Ellicott Dredges – approached us and was looking for a metal fabrication contractor that could build a large stainless steel mining dredge. As a provider of customized metal fabricating, Bassett Mechanical has the capabilities and expertise to fabricate just about anything, like a 90,000-pound mining dredge.
